We Are Off to a Pipe Organ Factory!
- Nate and Lori
- Apr 27, 2018
- 7 min read

“To my eyes and ears the organ will ever be the King of Instruments.”
Wolfgang Amadeus Mozart
State 35: Kansas - March 27, 2018
Lori
We woke up at a Walmart in Lawrence well rested and ready for a brand new day. Yesterday, we visited the National Teachers Hall of Fame & Memorial for Fallen Educators, and we could not wait to see what adventures lie ahead. Today, we drive across town to the Cross Country Couple's “Made in the USA” tour for Kansas; Reuter Organ. Founded in 1917 by A.C. Reuter, Earl Schwartz and Henry Jost, the Reuter Organ Company has designed and built over 2240 pipe organs for concert halls, funerals homes, universities, theaters, synagogues, private residences and of course churches. For over 100 years, Reuter has created state of the art instruments expertly merging new age technology with time tested hand crafted artistry to make music instruments lasting for generations.

I was very excited to learn how a pipe organ is made. My late grandmother Anna Marie Dittus played the pipe organ in church for over 40 years. Although, I took lessons as a child, I am hardly an organist. During my week in Nebraska, I had a chance encounter with a 100+ year old pipe organ in a church, and seized the opportunity to strike a few chords in my Grandma’s memory. You can read more about it clicking here. The above is a picture of my Grandma and I. She is in heaven, and I miss her very much.
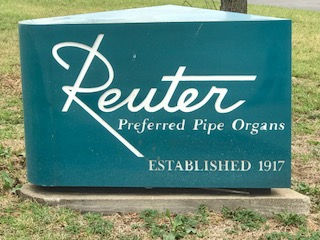
After parking Rosie, we made our way towards the main entrance of Reuters factory, and were greeted in the lobby by our guide Tom. A 30 year Reuter employee, Tom was a middle aged man with a pleasant disposition, and clearly possessed a passion for his craft. I could not help but notice Tom had a striking resemblance to the host of the Home Improvement TV show “This Old House” Bob Vila. Tom began by explaining the products and services Reuter offers. In addition to constructing new pipe organs, Reuter also restores, repairs, and even performs “organ transplants”! Tom assured me he had no intention of checking my driver’s license for my donor status. When orchestrating an “organ transplant”, Reuter matches organs from defunct businesses with those who are in need of an instrument. Reuter can transport, repair, and even adapt any pipe organ from the old location into its new home! Not only is the cost of a transplanted organ significantly less than constructing a new one, doing so preserves the history and legacy of each instrument. Apparently, pipe organs have a very long shelf life! Exactly how long you ask? Located in the Basilica of Valere in Sion, Switzerland, the world's oldest, most original, and playable pipe organ was built in 1435! Ahh! A new addition to my bucket list! With regular maintenance, a quality built pipe organ can produce music for centuries! How many of today’s electric keyboards do you think will still be around in 500 years?
A pipe organ makes music by forcing pressurized air from a wind chest through pipes selected by striking a key on the console. Simply stated, the pipe organ is a big box of whistles, but in actuality, this powerful, versatile, inspirational and ancient instrument is infinitely more! The pipe organ has many distinct advantages over most other instruments. For example, a trumpet can only produce notes until the musician runs out of breath, and the notes of a piano slowly dissipate as soon as a key is depressed. However, the pipe organ's continuous supply of wind allows a note to be played for as long as the organist presses the key. Furthermore, a pipe organ is a versatile instrument, which can double as a dozens of different instruments. More on that a little later!

Reuter has four departments tasked with the construction of a pipe organ: engineering, woodworking, pipe making, and assembly/shipping. On average, the entire process from conception to installation takes six months. Naturally, we began by exploring the engineering department. Since each pipe organ is custom built, a representative from Reuter personally visits the potential client to assess the: building's architecture, existing acoustics, size of the space, specific instrumental needs and client budget. Next, a design is created, and a proposal is submitted to the potential client. In the old days, pipe organs were hand designed using drafting arms, straight edges, compasses, templates, electric erasers, and pencils. Nowadays, much of the design process is performed on computers. However, Reuter still has their old drafting tables and even retains all of their drawings of previously constructed pipe organs! What was once intended as an architects schematic, can now best be described as a work of art. These drawings are so spectacular they should be framed and hung on the wall!
Next, Tom led us into the woodworking area of Reuters factory. The console of a pipe organ not only contains the most wood components, but also serves as the instrument's focal point. Building a functional and aesthetically pleasing organ console begins by using the highest quality materials. From poplar to mahogany, before us stood stacks of beautiful solid hardwood boards just waiting to be transformed! From milling, sanding, cutting, routing, joinery, and finishing, each of the pipe organs wood components are expertly constructed by Reuter's carpenters. One noteworthy observation I made in the woodworking area was the old age of the tools. I felt like I was having a flashback to my Grandpa’s workshop! Tom shared many of the tools are original to the company’s founding in 1917! Reuter pipe organs are built using a process which has stood the test of time. The tools used during construction are an integral part of that process and part of the company’s legacy. Nothing gets replaced unless absolutely necessary! Please see the pictures below.
Next, we headed into Reuter's pipe making department. Since every pipe organ is custom made, the number of pipes can range from a few dozen to over 20,000! The smallest pipe measures less than an inch tall, and produces a sound so high pitched it will drive your dog crazy. The largest pipe can measure 32 feet tall and produce a sound deep enough rattle the windows! With very few exceptions, Reuter makes all of their pipes in the factory. The process begins by smelting their own metal, which is poured into molds to form long thin metal sheets. Depending on the design, the metal sheets are cut into hundreds, and in some cases, thousands of distinctly different sizes. Next, the piece of cut metal is run through a machine to form a contour, and the seam is hand welded to form a pipe. Now, the process repeats upwards of 20,000 times for each organ! The amount of time, patience, organization and craftsmanship necessary to create a single organ pipe was astounding! Please see the pictures below.
Next, Tom brought us into his workshop where he proudly proclaimed, “Here is where the music is made”. Please be advised, the following is a grossly oversimplified explanation on how a metal tube is transformed to play a single musical note. Tom cuts a slit in the side of the pipe, and manipulates the metal opening to produce the desired sound. In the workshop, Tom has a tuned pipe organ. He takes the newly formed slitted pipe, and connects it to the organ. Utilizing decades of expertise, he compares the note he played on the organ to the sound produced by the new slitted pipe, and then he repeats the process upwards of 20,000 times for each organ! As a musician and organist, Tom's sensitivity to pitch and sound was amazing! On the wall of the workshop were over 100 different pipes bent and contorted in the strangest and most peculiar manner. Tom explained each pipe produces a sound mimicking various instruments such as a french horn, tuba, trumpet, bassoon, oboe and dozens of others making the pipe organ one of the most versatile instruments in the world. Please see the pictures below.
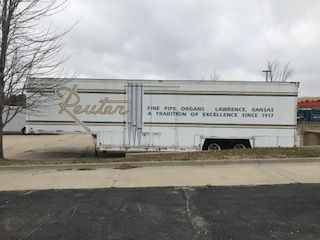
Our tour concluded in the Reuter's packing and shipping department. Depending on the size of the instrument, a pipe organ can consist of over tens of thousands of individual parts. In the packing and shipping department, the finished pipe organ is assembled, and undergoes final inspection for aesthetics and functionality. The organ is then disassembled, carefully packed for shipment and loaded on a truck to be installed in its new home.
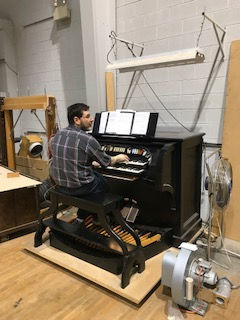
Tom had one last surprise for us prior departing. In the far corner of the shipping area was a pipe organ with a fascinating history. This particular pipe organ was built by Reuter in the 1920’s, and was installed in a silent movie theater in New Mexico. One day, Reuter learned the theater was scheduled for demolition, and employees of Reuter sprang into action to preserve a piece of their company’s history. The organ was brought back to the Reuter Factory for restoration. After sharing the story of the rescued organ, Tom sat down at the console and graciously and expertly played us a song!
Long at last, the finished product! Seeing a picture of their installed organs is one thing, but experiencing a pipe organ played by a trained musician is an entirely different experience. We noticed one of the pipe organ pictures was from Fairfield, CT. Since our former home state of Connecticut will be the 48th state on our journey, we will make a point to visit this organ in person! Please see the pictures below of Reuters Pipe Organs.
Since we have no room for a pipe organ in a 76 sq. ft. van named Rosie, the Cross Country Couple is clearly not Reuter's target demographic. Nevertheless, Tom spent almost 2 hours educating us about the construction of pipe organs, introducing us to the dedicated employees who produce a quality product made in the USA, and serenaded us with song before we departed. Tom, you are an expert craftsman, an exceptionally talented musician, and a really great guy!
Today, most associate the pipe organ with church services, or early Hollywood horror movies. Moreover, with the dawning of the digital age, many view the pipe organ as an obsolete relic from a bygone era, but nothing could be farther from the truth. While the pipe organ is an ancient instrument dating back to the 2nd Century B.C., its ability to survive through the ages and find a niche despite vast cultural changes over the millennia reinforces the relevance of this immortal instrument. Lada Gaga’s; “Poker Face”, Guns N' Roses; Sweet Child O' Mine”, and Michael Jackson’s; “Billie Jean” and “Beat It”, are just a few of the songs by today's biggest stars adapted to be played on the pipe organ. Listening to the aforementioned songs on “You Tube” performed on the pipe organ was quite the breathtaking experience! But don’t take my word for it. Click here to listen for yourself! See, Mozart was right when he hailed the pipe organ as “King of the Instruments”!
After departing Reuter Organ, we drove 52 miles North to Atchison where we found a Walmart to spent the night.
Comments